
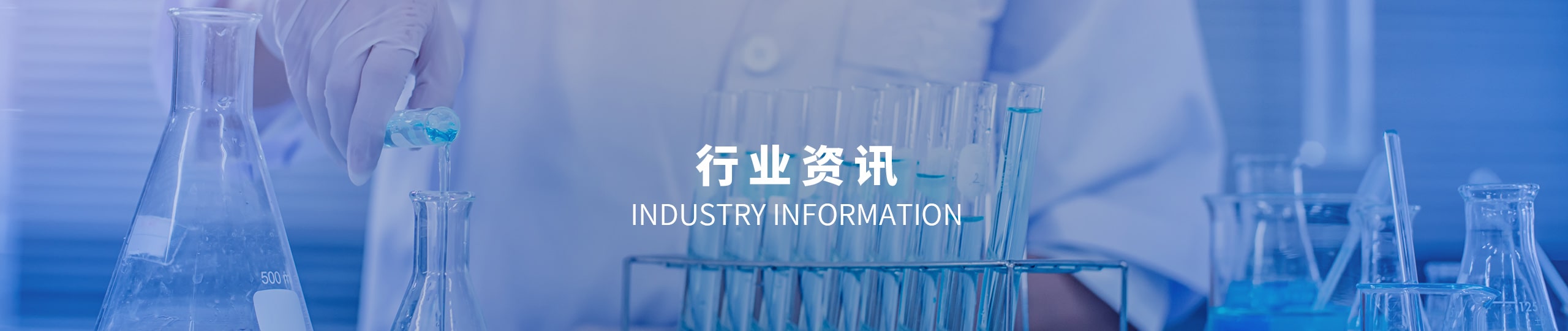
天然橡胶配方研发
来源:本站 发布时间:2021年04月08日
天然橡胶具有许多可贵的性能,在合成橡胶大量出现之前,天然橡胶是橡胶工业及其制品的万能原料,有“褐色黄金”之称。简单地讲,天然橡胶实际上是天然胶乳浓缩凝固而形成的,其中,橡胶烃的化学结构主要是顺式1,4- 聚异戊二烯(约占 98%),其分子结构如下:
天然橡胶的基本特性
1 、 物理特性
(1)天然橡胶无一定熔点, 加热后慢慢软化, 到 130-140℃时完全软化以至呈熔融状态;到 200℃左右开始分解,到 270℃则急剧分解。
(2)天然橡胶的玻璃化温度为 -74~ -69℃,在常温下稍带塑性,温度降低则逐渐变硬, 0℃时弹性大幅度下降, 冷到 -70℃左右则变成脆性物质。受冷冻的生胶若再加热到室温, 则仍可恢复原状。
(3)天然橡胶具有很好的弹性, 弹性模量为 2~4MPa,约为钢铁的 1/30000。弹性伸长率最高可达 1000%,回弹率在 0~100℃范围内可达 70~85%。
(4)天然橡胶是一种结晶性橡胶,自补强性大,具有非常好的机械强度,纯胶硫化胶的拉伸强度为 17~25 MPa,而经炭黑补强的硫化胶则可高达 25~35 MPa。在高温 (93℃ )下的强度保持率为 65%左右。
(5)纯胶硫化胶的耐屈挠性较好,屈挠 20 万此以上才出现裂口,这是由于天然橡胶的滞后损失小,在多次变形时生热低的结果。
(6)天然橡胶是良好的电绝缘材料,除去蛋白质后电绝缘性能更好,体积电阻可达 1017Ω .cm ,且潮湿或浸水条件下也变化不大。
(7)天然橡胶具有较好的气密性。
2 、 化学特性
(1)天然橡胶因有不饱和双键,是一种反应性较强的物质,每一个双键形成一个反应活性点,它们分布在整个橡胶分子的长链中,支配着橡胶的化学变化,其反应可分为加成、取代、环化、裂解等,由此可变成硫化胶和其他多种改性天然橡胶或天然橡胶衍生物。天然橡胶与硫化体系均匀地混合,在一定温度和压力下反应一定时间,就会由线型结构的生胶转变成网状结构的硫化胶。
(2)天然橡胶在空气中容易与氧进行自动催化氧化的连锁反应,分子链断裂或过度交联,橡胶发生粘化和龟裂,使橡胶的物理机械性能下降,这就是橡胶的老化。光、热、屈挠变形和铜、锰、铁等金属都能促使橡胶老化。未加防老剂的天然橡胶在强烈阳光下曝晒 4~7 天后就会出现龟裂现象,若与一定浓度的臭氧接触,甚至在几秒钟内就会发生裂口。不耐老化是天然橡胶的致命弱点。然而通过添加防老剂,可以大大改善天然橡胶的老化性能,使其在阳光下曝晒两个月看不出有多大的变化,在仓库中贮存 3 年后仍可照常使用。橡胶在高温下老化速率加快, 一般按温度每增加 10℃老化速度加快 1 倍的规律变化。如使用温度超过 130℃,则天然橡胶的使用寿命将大大缩短。
(3)在低温下长期贮存时,天然橡胶容易结晶变硬;在 0℃左右,硫化胶结晶达到 50%左右约需 37 天,而生胶仅需 6 天。但是,这种结晶是可逆的,一经升温橡胶又会恢复到原来的弹性状态。
(4)天然橡胶为非极性橡胶,因此,它能耐一些极性溶剂,但却不能耐油和其他非极性溶剂。
另外,天然橡胶具有较好的耐碱性能,但不耐浓度较高的强酸(如 10%的硝酸、 37%的盐酸、 50%的硫酸等)。
3、天然橡胶的配合
天然橡胶生胶一般不能直接用于生产制品,而必须添加各种配合剂制成混炼胶,并经硫化后才能满足各种实际使用条件的性能要求。根据天然橡胶制品的应用要求,科学合理地选择各种配合剂(确定其类型和用量等) ,使天然橡胶材料具有符合应用要求的物理机械性能、 良好的加工工艺性能和较低的制品成本,这一过程我们就称为天然橡胶的配方设计。
天然橡胶主要的配合体系包括:硫化体系、促进剂体系、防护体系、补强填充体系等。
硫化体系
天然橡胶适用的硫化剂有 :a.硫、硒、碲;b.硫磺给予体;c.有机过氧化物;d.酯类;e. 醌类等。
一般要根据不同的性能要求采用不同的硫化体系。
1 、 硫黄硫化体系
采用硫磺硫化是天然橡胶加工中最传统的方法,根据硫化体系中硫磺和促进剂配比的不同,硫磺硫化体系可分为普通硫化体系、半有效硫化体系和有效硫化体系三种。
普通硫化体系又称传统硫化体系,是采用高量硫磺和少量促进剂配合的硫化体系。硫磺的标准用量为 2.75 份 (每 100 份 NR) 。这种硫化胶的单硫键较少,而多硫键则高达 70%以上,由于多硫键的键能低、稳定性不好,所以硫化胶的耐热和耐老化性能较差,即使加入大量防老剂也无济于事,但是这种硫化胶的综合物理机械性能较好
2 、 硫磺给予体硫化体系
天然橡胶常用的硫磺给予体有秋兰姆类和二硫代吗啡啉 (DTDM) 。
秋兰姆类(如二硫化四甲基秋兰姆 TMTD 、二硫化四乙基秋兰姆 TETD 、四硫化四甲基秋兰姆 TMTT 等)在硫化温度下能释放出活性硫, 故可作为硫化剂, 使胶料不加硫磺即可硫化 (所谓的 “无硫硫化”)。其中 TMTD 使用较多。但是,使用秋兰姆的胶料有易喷霜和焦烧时间短的缺点。
二硫化二吗啡啉 DTDM 常用于半有效和有效硫化体系。在硫化中, DTDM 完全取代硫磺时, 就形成有效硫化体系;若取代部分硫磺,则形成半有效硫化体系。配合 DTDM 的天然橡胶胶料的焦烧时间长,不喷霜,不污染,硫化胶物理机械性能良好。
3 、其它硫化体系
酯类硫化体系是指氨基甲酸酯交联体系,它是二异氰酸酯( TDI、 MDI )和对亚硝基苯酚的加成物(对醌单肟氨基甲酸酯) ,能赋予天然橡胶良好的抗返原性、耐热性和耐老化性。可改善天然橡胶与帘线、织物、钢丝和其他材料的黏合性能。
酰亚胺硫化体系属于高温硫化体系,硫化胶的抗返原性和热稳定性好,并且压缩永久变形小,与玻璃纤维的黏合性好,可作为硫化剂的马来酰亚胺主要有 N,N`- 间亚苯基双马来酰亚胺、 4, 4`-亚甲基双马来酰亚胺、 2, 6-二叔丁基 -4-(马来酰亚胺甲基)苯酚以及 4, 4`-二硫代双苯基马来酰亚胺等。其中以二硫代双苯基马来酰亚胺和间亚苯基双马来酰亚胺效果最好。
天然橡胶可以用有机过氧化物硫化。最常用的有机过氧化物为过氧化二异丙苯 (DCP)。DCP 用量为 2~ 4 份,硫化胶形成的交联键为碳 -碳键。硫化胶具有好的热稳定性和优异的耐高温老化性能,蠕变小,压缩永久变形小,动态性能好,抗返原性好。缺点是胶料硫化速度快,交联效率高,硫化胶抗动态疲劳性能好。
该类品种有聚( 2-二乙氨基双 -4, 6-二硫醇基三嗪) 、聚( 2-六亚甲基双 -4, 6-二硫醇基三嗪)和聚( 2-N-甲基环乙基氨基双 -4, 6-二硫醇基三嗪)。
天然橡胶硫黄硫化体系通常要配用氧化锌 2~ 5 份、硬脂酸 1~ 3 份等活性剂。
4、促进剂体系
促进剂与硫化剂配合能起到使硫化剂活化、加速硫化反应、缩短硫化时间的作用。天然橡胶常用的促进剂主要有二硫代氨基甲酸盐类 (如促进剂 ZDC、 PZ 等)、秋兰姆类促进剂 (如促进剂 TMTD 、 TETD 等)、噻唑类(如促进剂 D、 DM 等)、次磺酰胺类(如促进剂 CZ、 AZ、 DZ 等)。
天然橡胶选用促进剂主要应考虑以下两点:一是促进剂的硫化临界温度,即促进剂在硫化过程中开始起促进作用的温度(见表 5-3)。一般地,临界温度低的促进剂易焦烧,但反应速度快;临界温度高的促进剂不易焦烧,在较高温度下才起反应。对于厚壁制品,为了防止胶料早期焦烧,宜使用临界温度较高的促进剂。
普通硫黄硫化体系(常规硫化体系,又称高硫低促体系)是采用高量的硫黄和低量的进剂配合的硫化体系,其交联键以多硫键为主,老化前胶料的通用物理机械性能较好,表现为强度高、弹性好、耐磨性高其成本低,但耐热性、耐老化性差,硫化时返原性大。由于天然橡胶不饱和度大,硫黄用量可比合成橡胶多,在软质橡胶制品中硫黄用量大约为 2~ 3 份,常用 1.75~ 2.75 份。促进剂用量在 1 份以下,硫黄用量在 2.5 份以上时,物理机械性能如拉伸强度、伸长率变化不大,而永久变形、硬度和定伸应力增加。使用促进剂有 M、 DM 、 CZ、 NOBS、 D、 TT 等,可以单用也可并用,常见并用形式有 DM 、 D/TS、 D/DM 、 M/H 、 M/TT 、 M/TS 、 CZ/TT 、 DM/D/H 、 DM/M/TT 、 DM/TT 、 CZ/DM 、 NOBS/DM 等等。
半有效硫化体系介于普通硫黄化体系和有效硫黄硫化体系之间。半有效硫化体系是由中等硫黄(1~ 1.7 份)和促进剂组成。交联键中既有多硫键也有单、双硫键。其硫化胶兼有耐热、耐疲劳和抗硫化返原等多种综合功能,因此获得广泛应用。典型配有 S/NS(1.5/1.5)、 S/NS/DTDM(1.5/0.6/0.6) 。
5)防护体系
天然橡胶是高不饱和橡胶,生胶及其橡胶制品在贮存和使用过程中,受到氧、臭氧、紫外线以及其他活性物质的作用而发生降解,拉伸强度损失,橡胶链发生交联硬化。为防止天然橡胶降解,添加防老剂是极有效的办法,良好的防老剂可以使橡胶制品的使用寿命提高几十倍。天然橡胶常用的防老剂有:胺类防老剂(防老剂 A、 D、 4010、 4010NA 、 4020 等)、酚类防老剂(防老剂 264、 SP等)、键合型防老剂(防老剂 NDPA 等)、以及石蜡等等。
6 )补强填充体系
依据配方要求,加入多孔粉石英填料可以提高胶料的物理性能,显示出较好的补强作用。其天然非晶态二氧化硅与其他硅粉相比具有细度高、活性高、比重轻的特点,因此它更易于同橡胶里的高份子等其他材料匹配融合。试验结果来看,该填料可替代部份炭黑、白炭黑降低生产成本。
在天然橡胶配合中要求耐磨时可加入超耐磨炭黑 (N110)、中超耐磨炭黑 ( N220)和高耐磨炭黑 ( N330)等。要求提高耐撕裂性时,以槽法炭黑效果最好。要求强度不高、弹性好、加工性能好时可用快压出炉黑( N550)、通用炉黑( N660)、半补强炉黑( N770)等。选用炭黑时,要注意炭黑的粒径、结构、表面活性和 PH 值, PH 值影响硫化速度,因此要根据炭黑的酸碱性,相应调整硫化体系的品种和用量。对炉法炭黑应选用后效性促进剂,且用量不宜太大。
对于浅色、艳色制品,天然橡胶可加沉淀白炭黑、活性白炭黑、超细多孔粉石英等作补强剂,加入沉淀白炭黑时应配有机活性剂二甘醇(一缩二乙二醇) 、甘油(丙三醇) 、乙醇胺、聚乙烯醇等调节硫化速度,用量一般为白炭黑用量 5%~ 10%。
补强剂用量可根据制品性能要求和含胶率指标确定,一般来说,要获得最高强度,用量 40~ 45 份为宜,用量过大,强度返而降低。若要求低强度、低成本,则可添加陶土、 CaCO3 等填充剂,以降低含胶率。
炭黑是最常用的补强剂,橡胶制品的性能与所选用的炭黑的性质是密切相关的,因此我们必须根据橡胶制品的性能要求来选用炭黑。一般而言,当要求提高橡胶制品的耐磨性能时,可选用超耐磨、中超耐磨和高耐磨炉黑;要求提高撕裂强度时,以槽法炭黑效果最佳;要求提高定伸应力时,可选用高定伸炉黑;要求高弹性时,可选用细粒子炉黑、中粒子热裂法炉黑;要求加工性能良好时,可选用快压出炉黑、通用炉黑、全用炉黑。另外,在选用炉黑时,要考虑炭黑的粒径、结构、表面活性和 PH 值等。
除炭黑外,白炭黑(化学成分是 SiO 2 )是另一种重要的补强型填充剂,它能提高天然橡胶的抗撕裂强度、减少龟裂扩展,改善胶料与帘布的粘合性能。
而常见的重 /轻质碳酸钙、二氧化钛、滑石粉、陶土等则属于非补强型填充剂,它们能增加胶料的容积和比重,降低制品成本。这些填充剂若经活化处理或添加偶联剂,有时也能获得一定的补强效果(如活性碳酸钙、用偶联剂处理的陶土等) 。
7 )软化增塑体系
1物理增塑剂
软化增塑的使用是为了获得良好的工艺性能,如黏性、柔软性,便于混炼、压延、压出成型等工艺操作,还可调节胶料的硬度。选择软化增塑剂要考 虑对物理机械性能的影响。软化增塑剂的常用品种有松焦油和固体古马隆,一般用量 4~ 5 份,石油系各类软化剂 5~ 15 份。
2 化学增塑剂(塑解剂)
天然橡胶中的烟片胶、绉片胶门尼黏度较高,给塑炼工艺带来一定困难,以往塑炼一般加入进剂 M和 DM 进行塑解,但效果不理想。添加化学塑解剂可以提高生胶的塑炼效果,缩短时间,提高效率。天然橡胶常用塑解剂有 SJ-103 和 12-I 等,用量 0.1~ 0.3 份。前者开炼机、密炼机都适宜,后者只适用于密炼机塑炼工艺。
上一篇耐高温PEI塑料改性
上一篇蔬菜催熟剂配方还原