
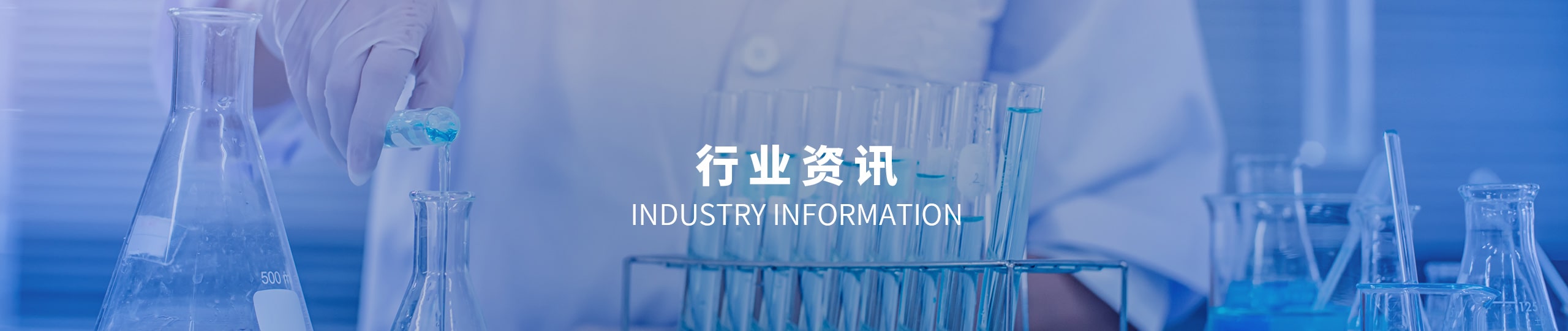
金属表面处理喷漆增加附着力
来源:本站 发布时间:2021年04月29日
一、脱脂:
(1)尽量避免采用高温强碱脱脂液
高温强碱对钢铁表面有侵蚀和钝化作用,能中和钢板表面的许多晶格点,形成氧化膜及氧化物,导致成膜时晶核的生长速度小于晶粒长大的速度,从而在数目不多的活性点上晶粒生长粗大,降低前处理质量和涂层的防护性能。而且脱脂液碱性强,清洗效果不佳。所以,对常(低)温除油应选用弱碱性脱脂剂。
(2)注意喷淋脱脂的操作要点
a.喷淋压力合适。虽然压力大,脱脂速度快,但当压力超过工件承受能力时,有可能造成工件变形。
b.设法减少喷淋槽中漂浮物和沉渣以防止吸入水泵而堵塞管道及喷嘴。
为此,喷淋槽应采用二级过滤(挡渣板和不锈钢网)
(3)控制脱脂液的浓度和温度
脱脂液浓度与它的种类有关,原则上预脱脂液的浓度高于主脱脂液,这是为了使油污尽量在预脱脂中除净,便于控制脱脂后水洗槽的污染度。但无论何种脱脂液其浓度过高都会引起表面活性剂盐析,而浮于液面或沉于槽底,失去脱脂能力,有时甚至比低浓度还要差。另处,温度对于脱脂效果也有影响,随着脱脂液的温度提高, 脱脂效果更好。但温度过高(≥80℃),会大大加速表面活性剂的水解速度,析出上浮,造成药剂的无谓损耗,脱脂效果反而降低,工件表面泛黄。一般加入阴离子型表面活性即可解决。
(4)温度降低,脱脂时间适当延长,脱脂效果变差
脱脂液浓度与它的种类有关,原则上预脱脂液的浓度高于主脱脂液,这是为了使油污尽量在预脱脂中除净,便于控制脱脂后水洗槽的污染度。但无论何种脱脂液其浓 度过高都会引起表面活性剂盐析,而浮于液面或沉于槽底,失去脱脂能力,有时甚至比低浓度还要差。另处,温度对于脱脂效果也有影响,随着脱脂液的温度提高, 脱脂效果更好。但温度过高(≥80℃),会大大加速表面活性剂的水解速度,析出上浮,造成药剂的无谓损耗,脱脂效果反而降低,工件表面泛黄。一般加入阴离 子型表面活性即可解决。
(5)防止工件脱脂后会产生钝化膜
工件脱脂后表面可能附有一些碱性物质以及部分阴离子表面活性剂,使晶核数目减少,转化膜变薄,产生白点(无膜)丝状、发花等缺陷。所以脱脂后必须充分水 洗,最好采用多级喷淋水洗。有许多厂家认为热水优于冷水,这对于氧化皮较厚的钢板和需酸洗的工件来说是有利的。但对于只需脱脂的工件来说是不利的。原因是 当工件离开热水进入滴水区时,表面干燥过快,接触空气中的氧气而容易生锈。所以一般采用冷水洗为宜。
(6)为了保证质量
a.水洗保持循环溢流,水洗槽pH值应维持在7-8之间。
b.浸洗工件不要露出水面,否则表面易乏黄、乏绿。水洗好的工件尽可能少在空气中停留,尽快进入下一道工序。一般要求工件离开脱脂槽,进入水洗、到硅烷处理工序最好不要超过5分钟。
c.针对目前很多工艺现状,水洗槽无循环溢流,水洗槽pH值难以控制在7-8之间,建议现场管理人员严格管控,经常开启循环排污泵以确保水质量。
二、酸洗
按目前现场工艺设计,酸槽使用化学药剂一般为工业硫酸。一般浓度为98%,相对盐酸而言,是种不易挥发性酸,可按各种比例与水混合,并放出大量的热能,因为浓硫酸的比重比水大,因此,在稀释时所放热能要及时散去,切忌将水往浓硫酸中加入。浓硫酸具有极强的吸水性和很强的腐蚀性,属于一种强酸,所以操作时应 注意安全作业。
硫酸在常温条件下,对铁锈的去除能力较弱,甚至提高硫酸浓度数倍也难以显著提高硫酸的除锈能力。当溶液中硫酸的浓度达到40%时,其除锈功能反而减弱,当溶液达到60%以上时,就几乎不能溶解氧化物,失去除锈功能,所以在使用硫酸除锈时,浓度控制在10-15%,温度控制在50-60℃时,除锈功能甚佳,在除锈过程中,为了使金属机体不产生过腐蚀现象,酸洗时应适量添加一些缓蚀剂,缓蚀剂的用量应严格控制,过量时容易影响酸洗效果。
针对目前很多工艺流程,酸洗后只有一道水洗槽,且没有循环溢流工艺,久而久之,酸洗后的水洗槽会比较脏,其危害性相当严重,容易造成窜槽现象。(就是说酸洗槽的残酸容易带入中和槽甚至硅烷槽)。为此,较为关注的是硅烷处理槽,因为硅烷处理槽的溶液属弱碱性,一旦受到残酸污染,就会把硅烷溶液中和掉, 破坏表面活性功能,导致硅烷槽液老化,硅烷处理膜层渗透较慢,甚至膜层无法反应,直接响硅烷处理质量;另外,如果酸洗后的工件残酸清洗不干净,直接带入硅 烷处理槽,就等于把硫酸根有害离子直接加入硅烷槽,导致硅烷处理槽液老化,难以调整,只能报废,会对生产质量造成严重负面影响及增加生产成本。
三、硅烷处理
(1)几何形状:
工件形状和结构越简单,对硅烷处理越有利。所以平面部位硅烷处理膜性能好,而折边部位、焊缝隙及拉伸部位等处的硅烷处理很薄或不连续,其耐蚀性相对较差。特别是焊件夹缝较多,容易导致夹缝处残酸清 洗不干净,硅烷处理后烘干,容易引起乏黄或吐酸反锈现象。
(2)工件表面状况:
钢板表面存在各种杂质(锈、油、污等金属离子)抑制成膜,造成局部硅烷处理不均匀,特别已经锈蚀的钢板无论采取何种除锈方法,其硅烷处理膜的耐蚀性差。另 外,工件表面粗糙,膜层疏松且均匀性差,耐蚀性低;反之,表面平整,膜层致密、均匀、耐蚀性好。因此,尽量不要选用已锈蚀的钢板工件来加工。同时要做到加 工过程中尽量不要破坏金属表面防腐膜,并加工后避免长时间露天存放。
(3)硅烷处理后:
硅烷处理后强调不用水洗,否则硅烷渗透膜会被水解掉,水解后的硅烷渗透膜影响耐蚀性和附着力,在湿热条件下易引起涂层的早期起泡和脱落;因此,特别强调硅烷处理好不能水洗,必须马上烘烤即可。
(4)硅烷处理膜:
硅烷处理膜经高温烘烤(180℃-220℃),膜层细化且更致密,耐蚀性能更好,且与基体的结合力有更大的提高,同时还可避免夹缝焊接处形成锈斑